VzBot 235 is a custom open-source 3d printer that provide an extremely high speed printing but still maintaning the high quality
Objectives
My main objective is to solve the problem of the current coreXY printer which is
the printing speed is too slow. In this printer I have implemented a microcomputer Raspberry Pi
with Klipper firmware to control the microcontroller ATmega2560 which can process the Gcode faster which partly lead to the goal. Secondly,
I have customized the X gantry with topology optiomization in SolidWorks and self-CNC with 3mm aluminum tube.
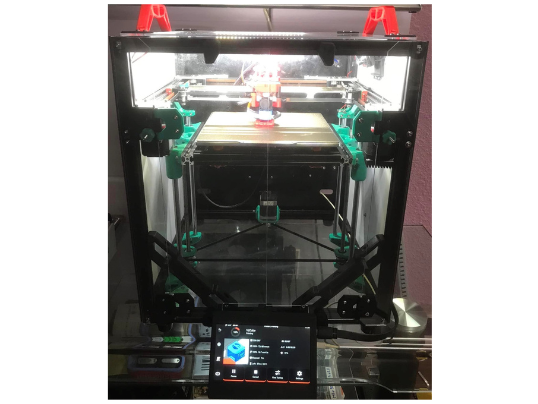
Overview
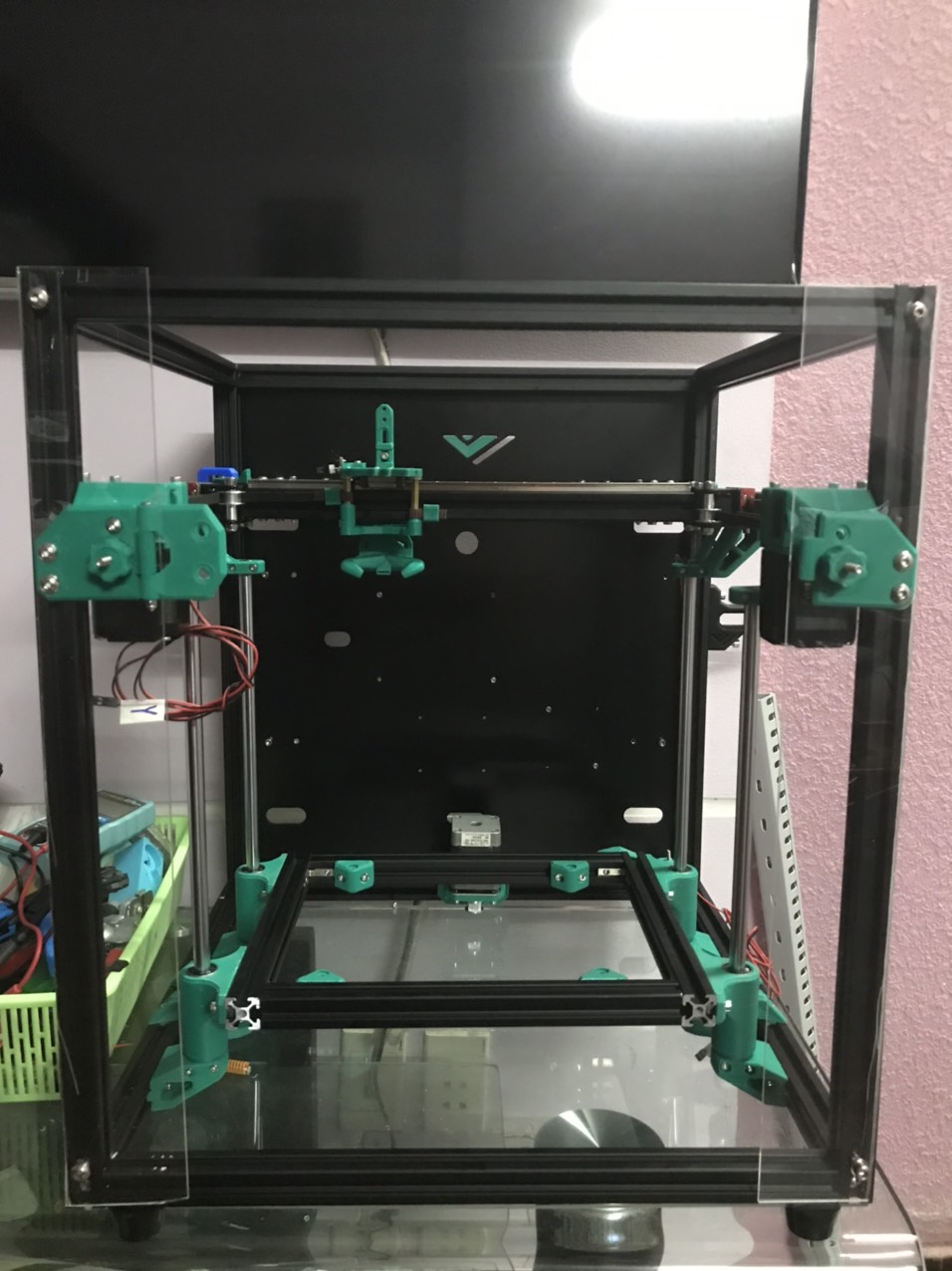
Building the frame
Testing the custom UI on LCD screen
Test print with the speed of 150 mm/s
In the video I have set up the printing configuration with the speed of 150 mm/s and the acceleration is 8000 mm/s^2 . The test prints are simple shapes: a square cube 30x30x30mm.
Outcome: The print completed four times faster than on the Ender 5/Ultimaker. Overhangs were flawlessly printed thanks to the efficient operation of the cooling fan. The surface maintains precision without any visible layering effects, ensuring stability without vibrations during printing.